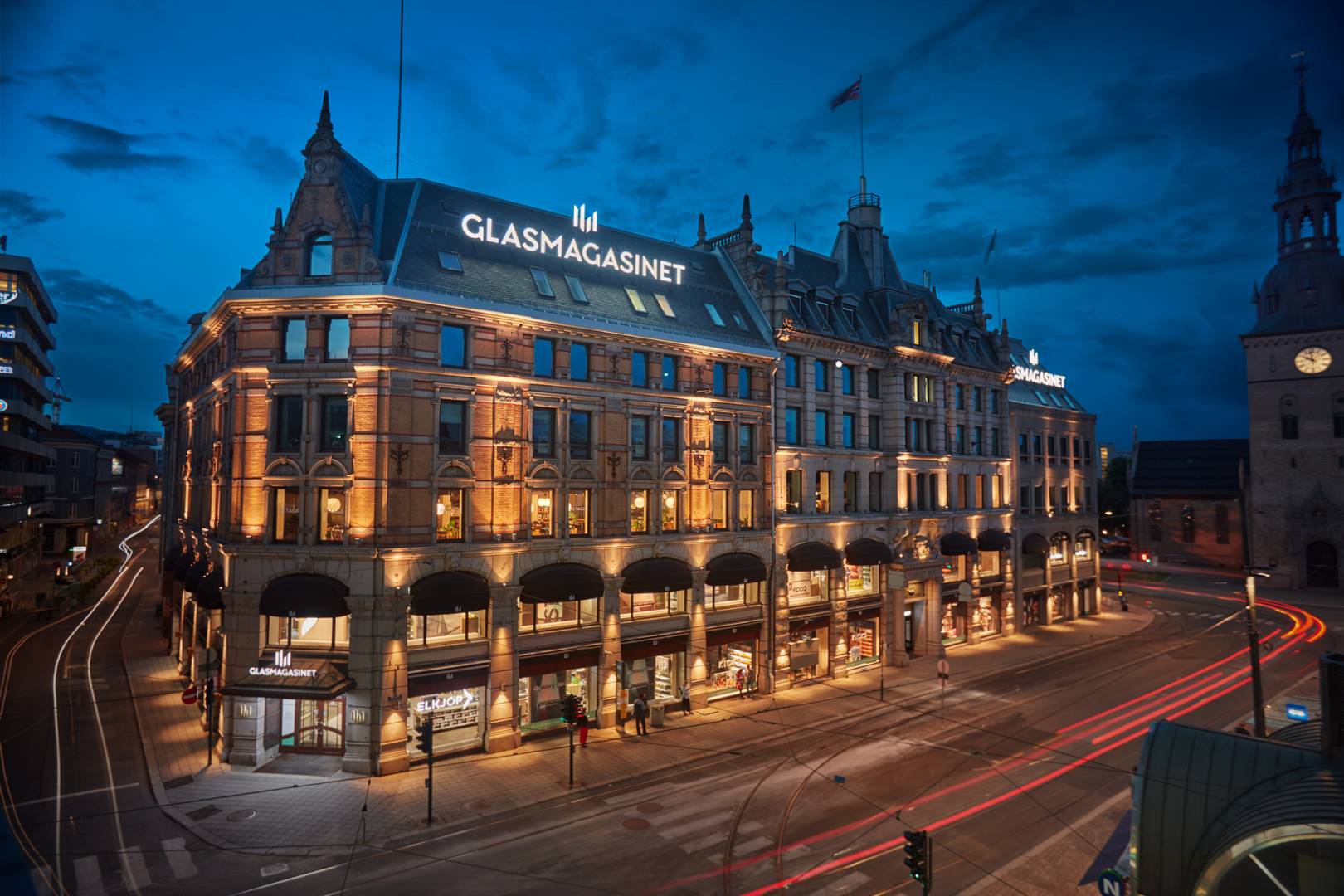
KLP Cuts Construction Design Management Time in Renovation
by 30%
Digital Construction Methods for Renovations
KLP Eiendom is one of the largest real estate companies in Norway, responsible for a whopping 1.7 million m2 of gross leasable area in Scandinavia. Their portfolio includes everything from hotels and shopping malls to large commercial buildings, with a particular focus on renovation projects.
These are usually buildings that need internal space improvements, or have new tenants who require changes for particular needs before moving in.
When it comes to these renovation projects, speed and efficiency are key to ensuring maximum net rentable time and predictable schedules for tenants. That's why KLP Eiendom places such a strong emphasis on short execution times and staying within budget.
Common challenges in renovations
A common problem often arises in refurbishment projects — Poor and imprecise As Built documentation in older buildings. Outdated architectural drawings make it difficult to identify and coordinate existing technical installations with new ones, like drainage pipes, leading to construction waste and costly surprises.
KLP Eiendom is investing in cutting-edge construction software tools, and laser scanning technology to ensure they can deliver accurate and precise data to improve sustainability in their construction projects.
By leveraging modern construction methods and digital twin technology, KLP Eiendom can mitigate construction disputes, eliminate costly delays, and ensure quality control in their projects.
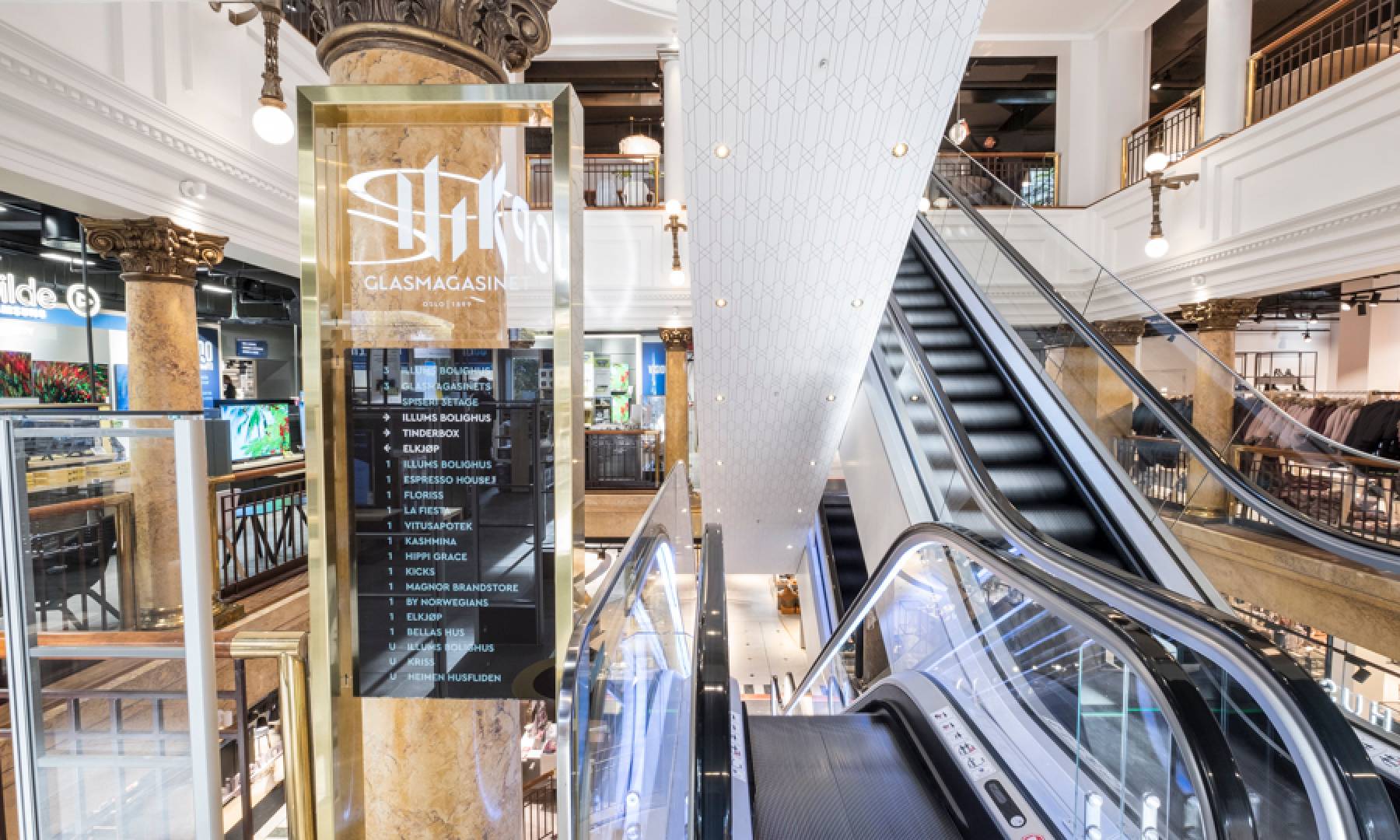
Cutting Design Time with Accurate As Built Data
KLP’s renovation of the Glasmagasinet Shopping Mall
Erik Skjønhaug, project manager at KLP Eiendom, chose Imerso to leverage laser scanning in KLP’s renovation of its shopping mall property Glasmagasinet. Our collaborative platform allows the KLP team to quickly identify and resolve critical deviations between the early construction drawings and the As Built reality onsite, reducing the design time by several weeks.
“Our work with building a correct drawing model became much simpler and more accurate, - says Lars Kittilsen, Architect at KLP. - Imerso reduced the need for emails and phone calls, and any issues were resolved more quickly."
Capturing As Built data early in the planning process
Through Imerso’s easy Laser Scanning workflows, the KLP team captured the onsite reality prior to the demolition phase, which enabled using Imerso’s construction quality control features to validate the design intent.
Any mismatches were automatically detected by Imerso’s algorithms and reported to the responsible partners. The design staff could use the platform to take measurements, screenshots from any perspective, and append comments directly to virtual objects, saving several trips to the jobsite.
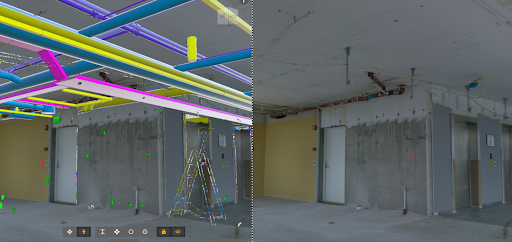
Benefits of Laser Scanning and BIM for Construction Management
Coordinating fieldwork with the BIM Plans
After construction kick-off at the site, everything must be done quickly and in a coordinated way. To ensure the work follows the BIM plans, laser scanning was used at planned construction milestones to document and verify the work status and quality. This enabled KLP’s architecture team to check critical elements in real-time, such as ceiling heights, interior plans, and the performance of the technical installations — from their browser at the office.
Real-time deviation detection
Using Imerso’s laser scanning data for automatic construction quality control, any detected deviations between the building plans and the physical reality were reported to the teams and fixed right away. This ensured that the work remained on schedule, without delays.
Updating the BIM Models to As Built
When any discrepancies were considered not relevant, the BIM model was quickly updated to ensure accurate As Built documentation, that KLP can rely for operating and upkeeping the property. The use of laser scanning and BIM in construction site management improved construction quality control, while enabling remote site monitoring.
.webp?width=1920&height=1200&name=KLP%20-%20GM%20scanINT-UI-min%20(1).webp)
Results at the Glasmagasinet Renovation
Time savings in Pre-Construction
Laser scanning the site before the project started saved valuable time in the process of establishing a good model for further design and BIM modeling. Imerso allowed what previously could take several weeks and many onsite inspections, to be compressed into only a few days.
Faster model geometry verification
With the automated checks provided by Imerso in hand, the KLP design team could understand all the structures present at the jobsite, to establish and verify the model geometry faster.
Imerso's user-friendly interface helped the team append notes and comments directly to real objects and take measurements with millimetre accuracy without needing to visit the site in person. This way, they could get the job done quicker and spend more time finding great, sustainable design solutions, and less time in manual measurements for detailing the basic model.
“Imerso reduces the time spent on surveys and inspections while giving a lower margin of error. By combining Imerso scans with BIMSync, we have an excellent tool for collaboration in the design process for the architects and executors, and a great opportunity to present projects and cases to customers.” says Lars.
Construction quality control and As Built documentation
Using Imerso for capturing onsite data during construction also offered a second crucial advantage: it provided accurate documentation to both KLP and the contractor teams.
Having As Built documentation in all phases of a project allows the parts to resolve potential conflicts earlier and reduce dispute costs. This reduces construction disputes and delays and prevents extra costs. Besides, the data remains available to KLP to use in future renovations, maximising efficiency in property management.
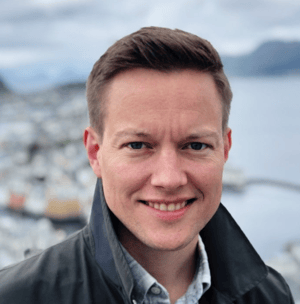
KLP Eiendom