.webp?width=1869&height=1045&name=sk%C3%A6rmbillede-2021-04-07-kl-11-48-08-min%20(1).webp)
Cutting Construction Rework and Delay Costs 10X in Denmark's Tallest Building
The Lighthouse Tower
Denmark has a new landmark to be proud of — The Lighthouse Tower is now the tallest building in the country. Standing at a height of 142 meters, the tower dominates the skyline of the city of Aarhus.
The construction of this modern landmark was anything but straightforward. The first phase of the project had been completed in 2012 when the terrace apartments were built. At that time however, the second phase was put on hold due to feasibility concerns regarding challenging ground conditions for such a heavy structure, alongside the looming menace of a financial downturn.
Per Aarsleff took the challenge
Per Aarsleff, a Danish construction company renowned for their expertise in groundwork, was awarded the task to build the second phase of the project. Besides the main tower, this second phase included the construction of two 10-storey buildings, "Promenadehuset" and "Kanalhuset".
Best practices in Lean Construction Management
The project was completed in 2022, with a stunning 142-meter-high iconic building now adorning the tip of Aarhus' harborfront, showcasing the future of construction.
Utilizing modern construction methods such as Lean Construction and digital construction tools, the project was completed with the aid of Imerso.
Imerso combines innovative methods like laser scanning and BIM into a real-time digital twin for highly efficient construction site management. Routine As Built surveys and proactive site monitoring helped ensure construction quality control throughout the project and ultimately avoid work errors and delay costs.
.jpg?width=4444&height=2438&name=Photo%20credits_%20Lighthouse%20United%20ApS%20and%20Mathias%20Daa%20L%C3%B8fquist%20(5).jpg)
Challenges in Construction Quality Control
Impressive in every way, the top of the tower gives public access to a viewing platform and a bar. The completion of the “Crown” of the tower, with its fantastic views of both the harbor and the city, was a major challenge in this project with a high risk of construction delay costs. Spanning 22 x 22 meters, the “Crown” consists of a heavy steel structure of over 70 tons, with a complex geometry resembling a seashell.
Prefabricated construction and curved roof structure
The idea was to lift the prefabricated structure to the top of the building after the top floors were completed. The steel elements were prefabricated and assembled on-site, then lifted up the tower in 4 parts. Once on the roof, they were placed on two different floors and bolted onto approximately 250 rods. Adding to the challenge, the roof structure has a stylish curved design with bends featuring eleven different slopes, making it difficult to place them correctly within tight tolerances.
Working on a tight schedule in a restricted space and unusual heights, the construction teams were left with little room for any deviations from the construction plans. Given such strict tolerances and time pressure, the team needed to ensure a lean construction process where every step can be checked before the next.
%203.jpg?width=1112&height=616&name=unnamed-min%20(1)%203.jpg)
Opportunity in Digital Construction
VDC coordinator Christian Øster and his team were looking for the right construction software tool to closely monitor the As Built status. The main focus was to implement an innovative workflow that emphasizes quality control, so any deviations can be detected early and resolved proactively.
From other projects, The VDC team at Aarsleff had great results using Imerso for capturing the As Built conditions with Laser Scanning — enabling all As Built data to be automatically verified against the BIM specifications on a routine basis.
Automation of As Built inspections — case example
Using a Leica RTC 360 laser scanner, the team made an As Built survey to capture the roof area where the tower “Crown” would be installed. Uploading the resulting As Built data to Imerso, Christian and his team ran the automatic inspection against the BIM models in minutes and found 14 deviations that had remained overlooked in that critical area alone.
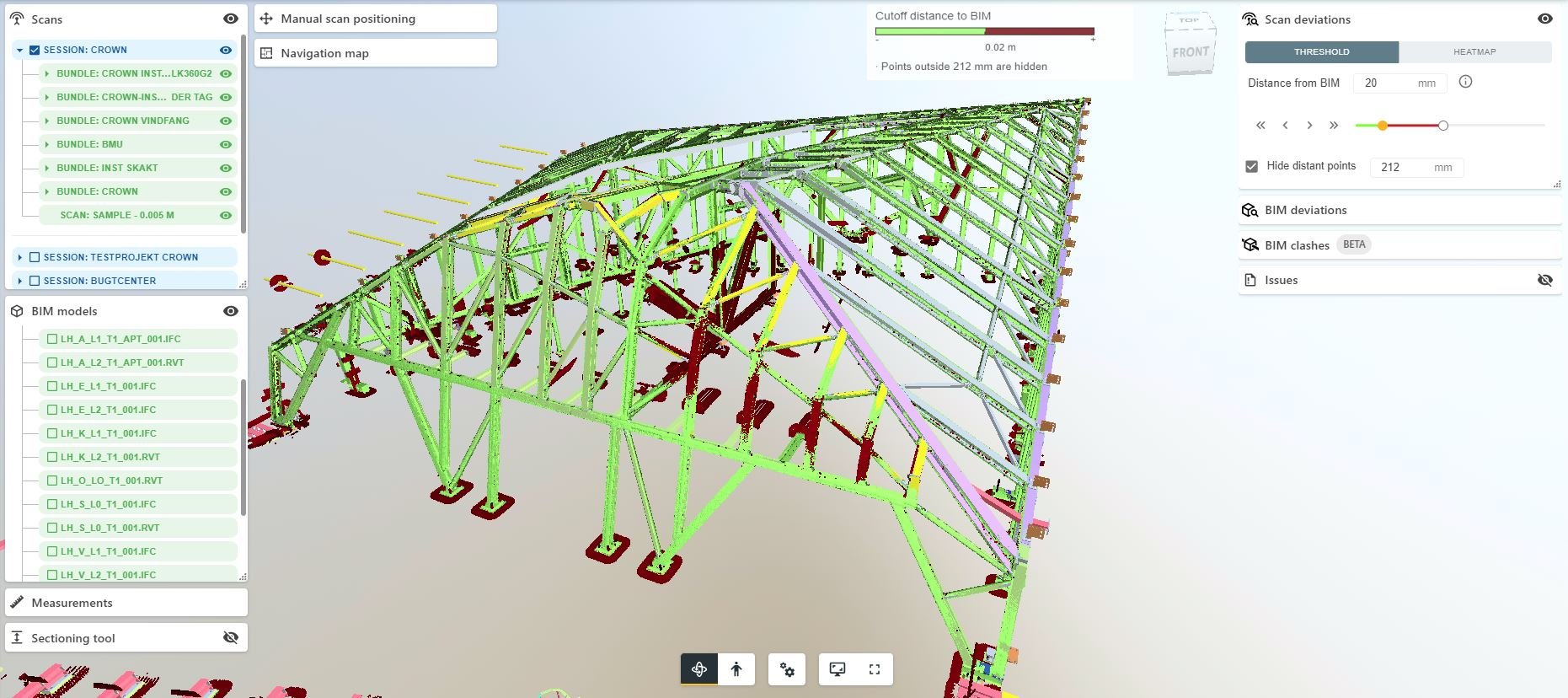
Scaling the Use of Digital Construction Methods
Aarsleff’s decision to use Imerso paid off, and the company is growing its adoption of the intelligent site monitoring technology — aiming to streamline best practices of Lean Construction and emphasize work quality through automatic BIM workflows.
Within eighteen months, Per Aarsleff has scaled up Imerso deployments across eleven projects with another two scheduled to start in 2023.
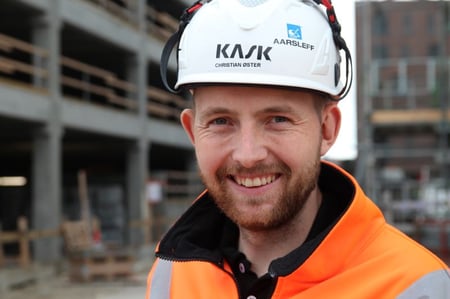
Per Aarsleff A/S