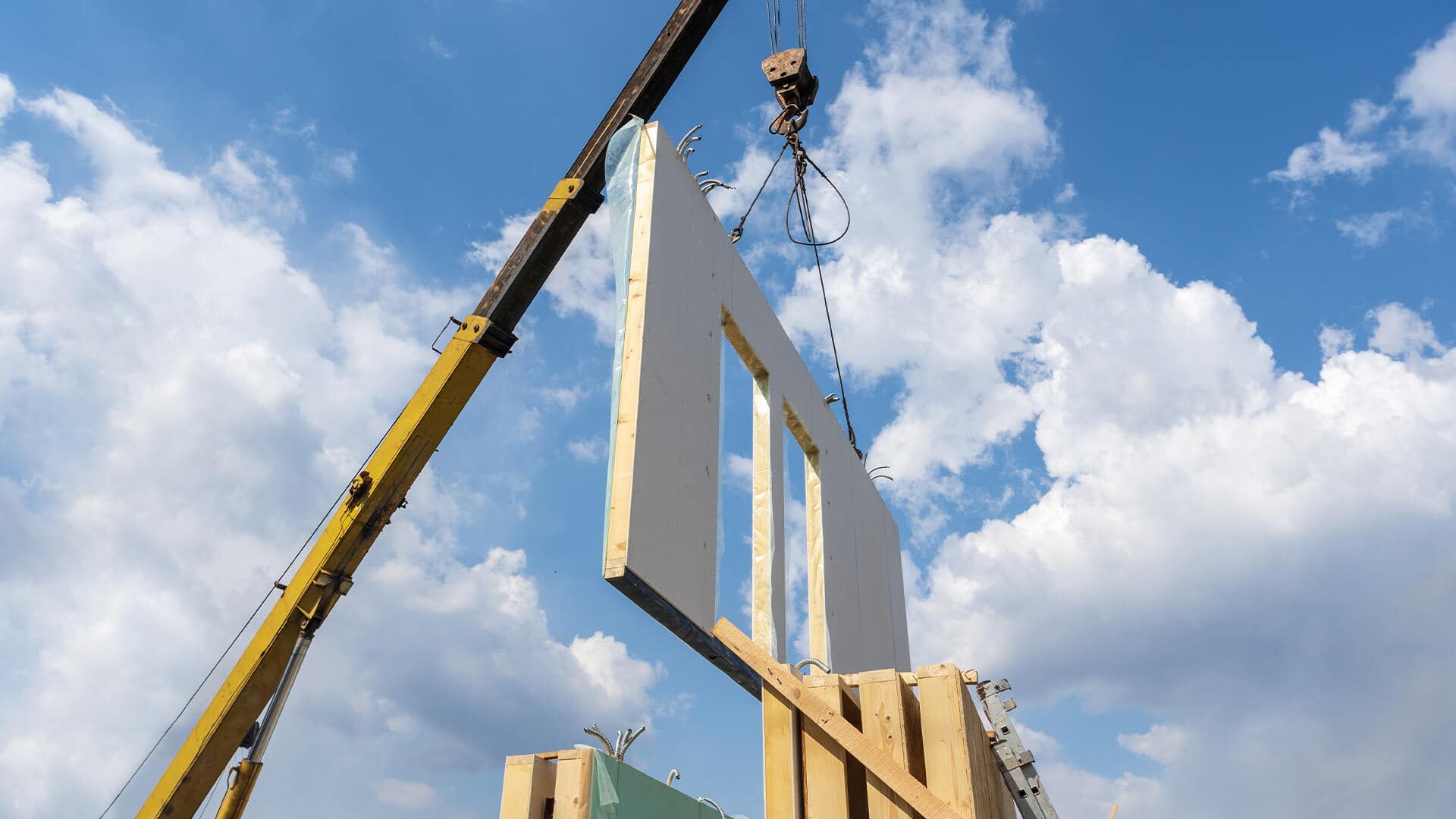
Byggstyrning Streamlines Prefabricated Construction with Imerso
About Byggstyrning
Byggstyrning is an innovative construction consultancy and early adopter of digital tools. The company’s ambition is to constantly improve their processes and find new ways to work smarter.
In their journey towards a digital construction process, the company was awarded the bSI 2020 Construction Award by BuildingSmart, in its recent Celcius project for its client Vasakronen – which Byggstyning concluded 2 months ahead of schedule and below budget, with 80% fewer rework orders, and zero accidents, through efficient use of OpenBIM tools.
Challenges with Prefabricated Constructions
In 2020, Byggstyrning was selected by Vasakronan, one of the largest real estate companies in Sweden, to take charge of managing the Folkungagatan 44 project - A 23.000 m2 commercial construction spanning seven floors in the heart of one of Stockholm's trendiest neighbourhoods. Once completed, the new office building will receive the LEED certification's platinum level – the greenest classification possible.
Several factors contributed to the challenge of managing this project.
Short deadlines
Working with a short deadline, the superstructure had to be prefabricated in parallel while the site was demolished and prepared for assembly.
Tight margins to neighbouring buildings
The construction was located on one of the major and busiest streets in Stockholm, with many surrounding buildings. The existing structures around the two ground floors had tight margins to the new building. The team had concerns of potential issues with fitting the prefabricated elements onsite when these arrive, and the risk of this halting the entire project.
Traditional construction inspection methods
Instead of the traditional methods of manual inspections and spot checks — which take days or even weeks, leaving several issues hidden — the Byggstyrning team sought a faster and objective examination method of the As Built conditions that avoids subjective evaluations.
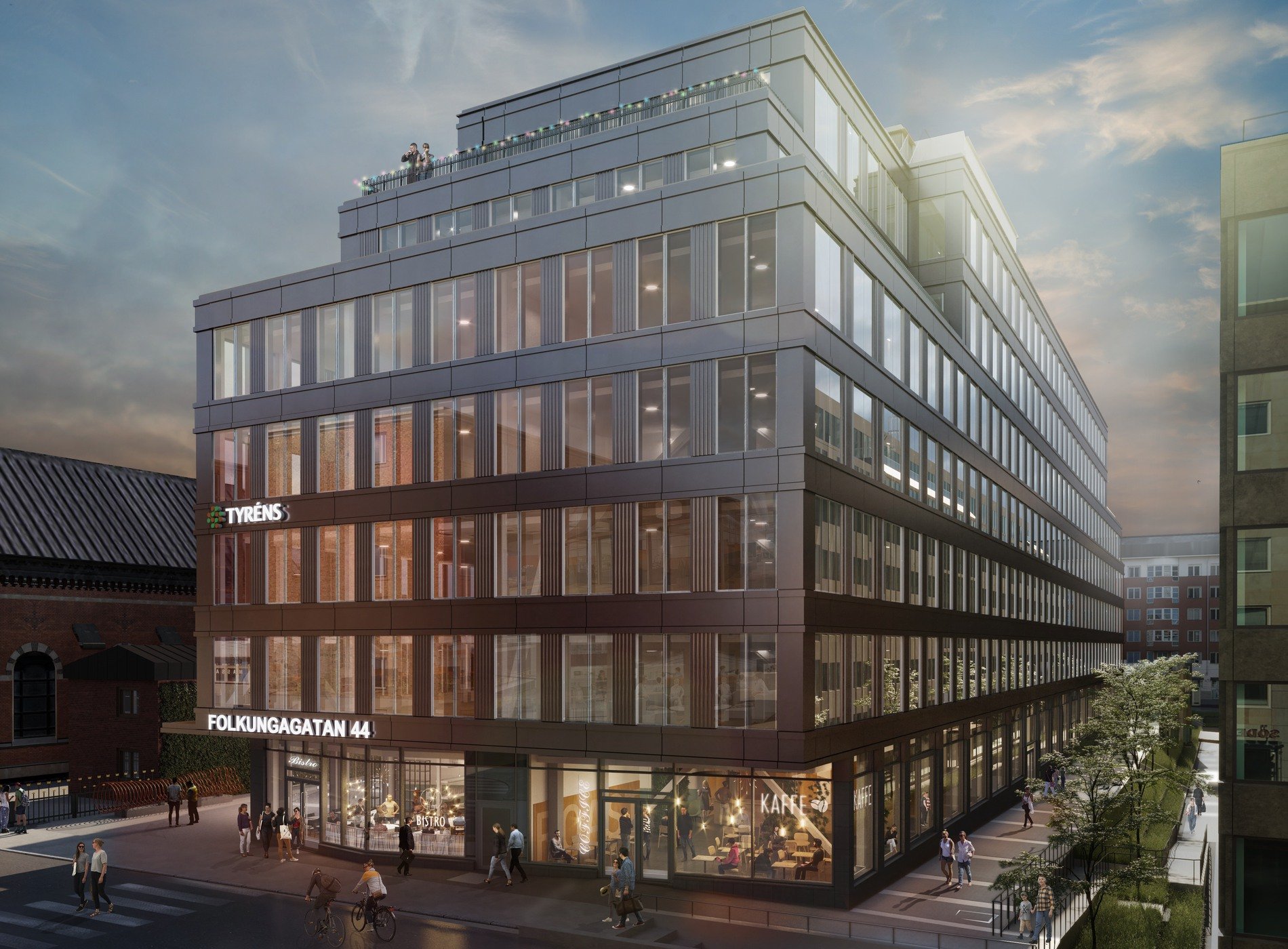
Eliminating As Built drawings with 3D Laser Scanning
The Byggstyrning team chose Imerso to capture the As Built status at the construction site and check it automatically against the building plans. By using 3D laser scan data, the platform benchmarks the onsite reality to the BIM plans and immediately catches any hidden problematic discrepancies.
Despite having no previous scanning experience, the Byggstyrning team leveraged Imerso’s app to turn such a traditionally complex process into a one-button workflow – as easy as taking a photo. Using a BLK360 laser scanner from Leica Geosystems, Johannes Ris, CTO at Byggstyrning, captured the onsite status on a weekly basis for instant inspection in Imerso.
This allowed to identify problematic areas early and adjust prefab elements offsite, while correcting misplaced onsite elements to ensure a frictionless fit across all prefabricated elements.
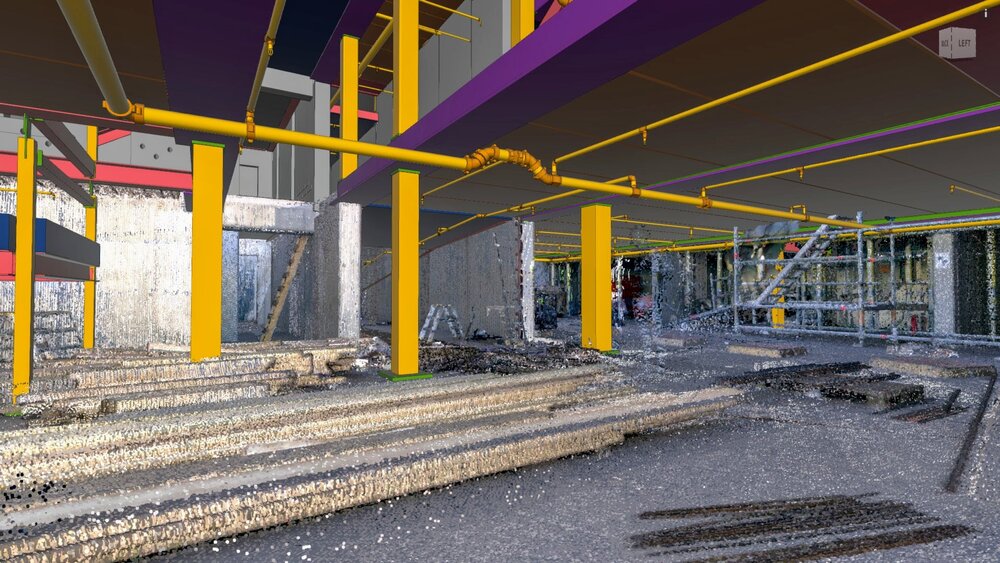
Results from Automatic Construction Inspections
The Byggstyrning team saw several benefits from using Imerso for routine As Built inspections.
Prevented clashes and delays proactively
The team was able to closely track the site status and work progress, clearly understanding any problematic areas well in advance in order to later place prefabricated elements without hassle and delays. Because Imerso had identified the issues early, the Byggstyrning staff could plan and order materials they knew they would need. This helped to keep the pre-defined schedule and the production flowing as planned.Improved efficiency and collaboration
With the 3D copy of the construction site accessible online, all staff could engage in the project and navigate the virtual jobsite together. This allowed having many more eyes and feedback on potential issues as early as possible, to accelerate information exchanges. The system allowed to vastly reduce the number of in-person visits to the jobsite, while still enabling the team to make faster decisions — saving time and costs.
Accurate BIM models updated to As Built
Discrepancies between the As Built reality onsite and the BIM building plans were corrected on the spot, through Imerso’s automatic BIM updating feature, to ensure correct As Built documentation in the final BIM deliverables.
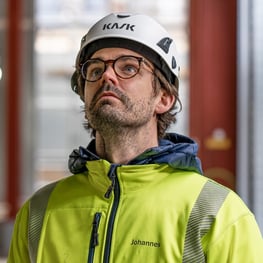